A revolutionary innovation, and not only because of its unconventional appearance, even for a pick-up. The Cybertruck, which until now has not been marketed in France or Europe, has made history in the automotive sector thanks to its revolutionary innovations. An example of Tesla’s capacity for innovation.
The first innovation that I would like to highlight is at the chassis level, which consists of a set of hundreds of steel pieces previously cut and stamped by suppliers, according to the car manufacturer’s specifications. For each part, specific tools must be developed and maintained over time, to guarantee the dimensions defined by the plan. As a former buyer of this type of parts at Valeo, I deeply understand the difficulty and efforts required to find suppliers capable of delivering the quality and quantity requested. Then, the manufacturer must manage all the logistics of these parts to be able to have them available on time at their assembly plant. There, an army of robots welds these pieces together. The chassis of a vehicle requires large investments and sophisticated logistics. It is a beautiful complexity. Tesla decided to change the situation and completely simplify chassis production.
An Italian innovation at the service of Tesla
Tesla engineers worked in cast aluminum. Since it is not technically possible to make the chassis in one piece to date, engineers designed three for the Model Y. But they still had to find a press powerful enough to mold 80 kg of cast aluminum. In 2017, the Italians from the company IDRA and its general director, Riccardo Ferraio, were surely the only ones who could meet the challenge. The “Giga Presse” has the dimensions of a building: it is 30 meters long, 22 meters wide, 14 meters high and weighs almost 400 tons. 80 kg of molten aluminum are injected into the mold at 850°C. Nearly forty-five pieces come out of the mold per hour, or about 1,000 pieces per day with a single press.
With this new production process, Tesla reduced the cost of the chassis by 40% and was able to remove 600 robots from its assembly line. The chassis is not only uniquely manufactured, but also directly houses the battery for reduced weight and better integration into the vehicle. Since then, the Italian company IDRA has sold twenty-four Giga Press around the world and not just to Tesla. Hyundai has already ordered this press and Toyota, the world’s leading manufacturer, has decided to adopt this production process. Thus, Tesla, with the help of the IDRA company, has revolutionized the manufacturing of automobile chassis.
Vehicle architecture revised by Tesla
Tesla has innovated again with the Cybertruck. It is the first vehicle to adopt a 48-volt electrical architecture, instead of the old 12-volt lead-acid battery. The 12-volt voltage was adopted by the automobile industry in the 1960s, even before the advent of electronics.
First, Tesla replaced the 12-volt battery, with an average lifespan of four years, with a 48-volt lithium battery that should last the life of the vehicle. We must not forget the massive increase of 87%. Tesla is the first manufacturer to take the step and make it a standard.
Tesla then reduces the current by a factor of 4 compared to 12 volt systems. Increasing the voltage is a necessity because the power demand for onboard electrical devices is constantly increasing, and at 12 volts, copper cables are thick, heavy and expensive, especially since the length of copper cables is measured in kilometers. in a car. Tesla thus achieves a massive profit and reduces its costs.
Finally, the control of all the car’s equipment goes through physical relays and fuses with a 12-volt battery. Finished with 48 volt architecture: control is digital. Furthermore, the reaction time has nothing to do with the fuses, in seconds, and the digital control, in milliseconds. The speed of execution of this new 48 volt architecture offers new combinations possible thanks to the software.
In conclusion, Tesla has not only been content to adopt automotive codes in terms of production, assembly or vehicle architecture. Tesla has reinterpreted and even innovated to gain efficiency.
Tesla has already managed to impose some of its methods on other manufacturers, which are proving more effective than traditional processes, such as Giga Presses. The 48-volt architecture will prevail over all automakers, it’s just a matter of time. In the history of the automobile industry, the Cybertruck will remain the first passenger vehicle to use a 48-volt architecture. Therefore, catching up with Tesla remains a challenge for all its competitors.
The Tesla book killed the car! was released on March 20 by Éditions Descartes & Cie
Source: BFM TV
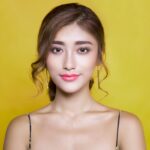