This is a question that often arises regarding the environmental impact of electric cars: what happens to the battery at the end of the vehicle’s useful life? If most of the time this essential organ begins a second life as a renewable energy storage unit, for example, there is also a recycling sector that allows the raw materials found there to be recovered.
A sector in full development, but for the first time a car manufacturer is launching into this activity. A year and a half after laying the first stone of its car battery recycling plant, Mercedes-Benz inaugurated this facility this Monday, October 21, a symbol of its commitment to electromobility.
Advancing in electrical
The factory is located in Kuppenheim, less than an hour’s drive from Stuttgart, the historic headquarters of Mercedes-Benz. An inauguration with great fanfare, attended in particular by the Chairman of the Board of Directors of the German group, Ola Källenius, and the German Chancellor, Olaf Scholz.
Despite the end of purchasing aid since the beginning of the year in Germany, causing a sharp drop in sales, Europe’s largest economy remains officially committed to the goal of ending sales of new thermal cars, including hybrids, between now and 2035.
“This factory combines two German passions: the automobile and recycling,” summarized Olaf Scholz before symbolically starting production with Ola Källenius.
A positive note in a Germany that seems to doubt its future in the electric car sector, with the Volkswagen crisis in particular. A national champion that no longer excludes having to close factories and eliminate jobs. A shock in a country so attached to its automobile industry.
A complex process
Despite these doubts, Mercedes remains convinced of the future of the electric car:
“This remains the driving force that will ultimately prevail; we are aware of the impact of the automotive sector on the environment,” underlines Renata Jungo Brüngger, member of the board of directors of the Mercedes-Benz Group, during a round table organized during this event.
The German brand thus does not question the goal of ending sales of thermal cars, including hybrids, in the European Union in 2035. And it is even preparing for an even more ambitious goal: carbon-neutral production between now and 2039.
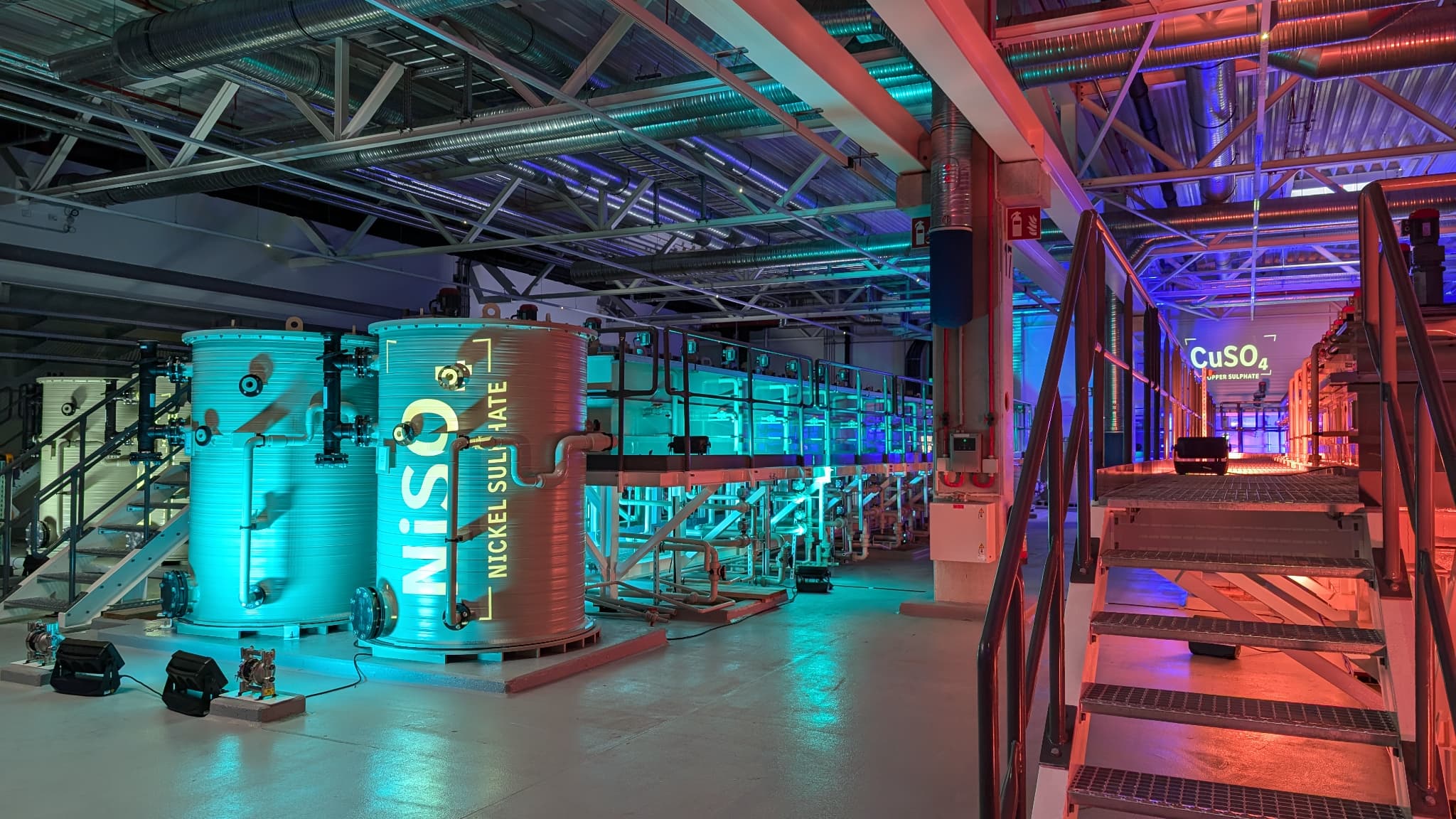
This ultra-modern factory fits into this framework, with a 6,800 square meter roof covered with solar panels that can provide up to 350 kW. And a green electricity supply for the entire site.
The factory should allow 96% of the battery modules to be recycled, recovering almost all the components found there.
The module to be recycled is first crushed before several stages that will last a total of two days: separation by air to isolate the plastic, copper and aluminum, and by electromagnetism for the iron. Then, passing through a press with a filter allows the graphite to be recovered on one side and the “black mass” on the other: a powdery black mass that will receive a chemical treatment to recover copper, cobalt, manganese, nickel and lithium.
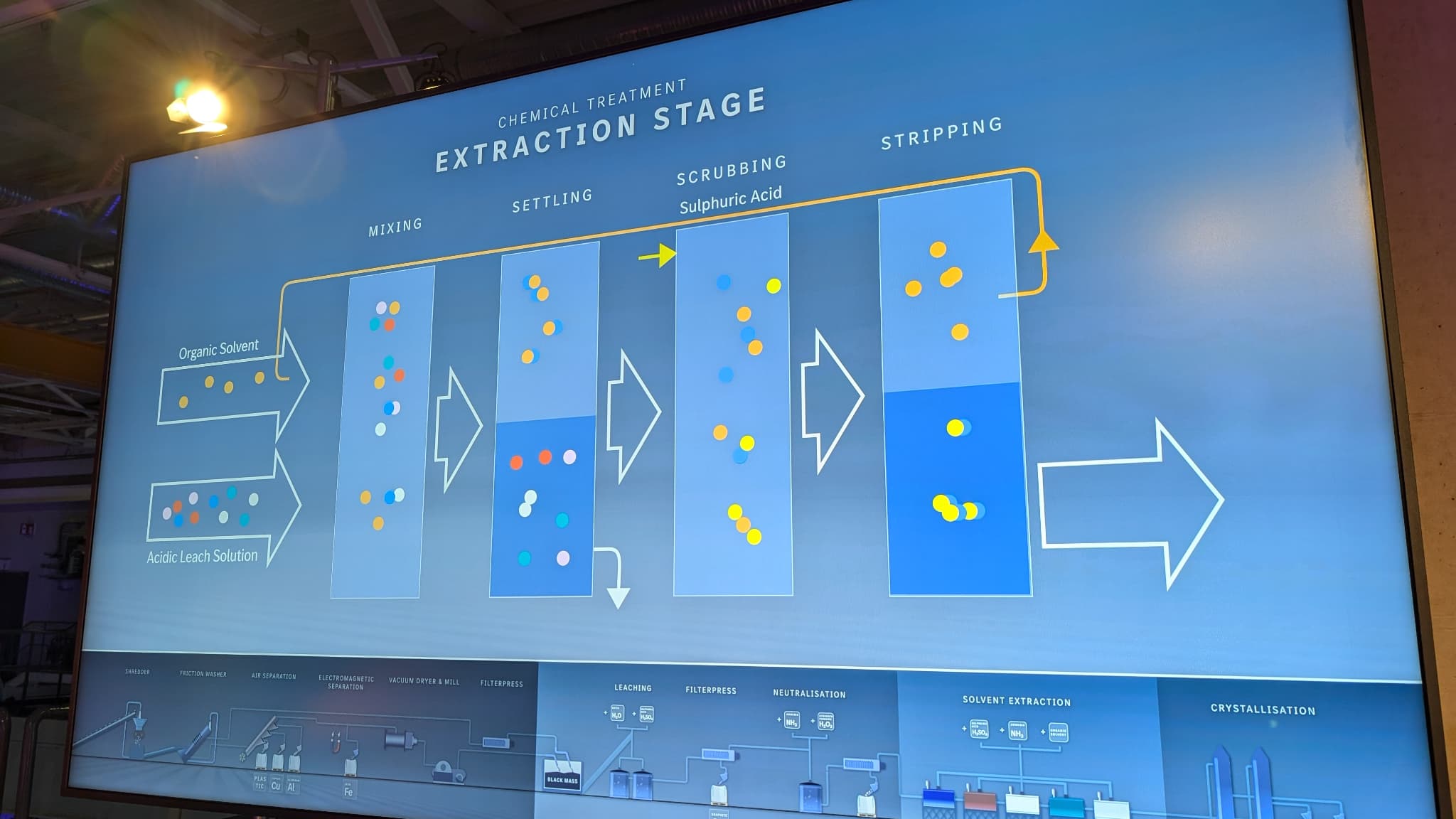
This process would significantly reduce the carbon footprint of an electric car, partly linked to the extraction of raw materials, according to Mercedes managers, who do not give precise figures. Enough to also benefit from a less expensive supply of resources for new battery cells.
Mercedes also insists on its choice of “mechanohydrometallurgical recycling”, which consumes much less energy than the pyrometallurgy that prevails in Europe today.
A pilot site for an activity of the future
The factory, however, remains a pilot site: Mercedes plans to initially produce 50,000 modules per year thanks to this recycling, that is, 2,500 tons. A module is a subset of a car battery. Thus, in a Mercedes EQE sedan there are 10 modules. Obviously, the factory would provide the batteries necessary for 5,000 cars, a drop in the ocean for the star brand that has sold more than 220,000 electric cars in 2023.
In comparison, the Swedish battery manufacturer Northvolt operates with its partners one of Europe’s main recycling plants, which will open in 2022 in southeastern Norway, with the capacity to process 12,000 tons of lithium-ion batteries per year, he recalls. the AFP.
But above all, Mercedes wants to be a pioneer in this area by moving forward. Currently there are few batteries to recycle because the cars are quite recent and the site initially only intends to process batteries from vehicles of its brand. Enough to better master this complex process and why not in the future be able to recycle modules from other manufacturers.
We can also point out that the German group is part of ACC, the joint venture with Stellantis and Totalenergies for the production of batteries, with the recent start-up of the Douvrin gigafactory. Two other partners who might be interested in this recycling prospect in the coming years.
Source: BFM TV
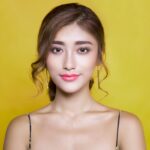