The restructuring of the global automotive industry, followed by the pandemic and the war in Ukraine, caused “serious difficulties” for Portugal’s mold industry. In just two years, the industry lost 38 companies and nearly 500 employees, out of a total of 498 companies with 10,400 employees. Between 2018 and 2021, sales fell by almost 200 million and while 2022 marks the reversal of the decline in production and exports, the erosion in the sector may not be over.
“Even with the expected growth of 3 to 5% in 2023, the adjustment process will continue, because there are many companies in great economic difficulties, as they have tried to lose weight without losing their key personnel. The rise in interest rates will do it which they ultimately cannot deal with,” admits Nuno Silva, Vice President of Cefamol – National Association of the Mold Industry.
At stake is an industry that grew from the middle of the twentieth century, divided between two major poles, in Marinha Grande and Oliveira de Azeméis, and in which Portugal is today “at the forefront” from a technological point of view, the organization and knowledge .
Born from the automotive industry, it is this development that gives a “massive growth boost” to the mold industry, which is currently about 80% dependent on the automotive industry, although it also produces molds for packaging, medical devices, household appliances, electrical equipment and electronics, furniture and aviation, among others.
2018 was the best year ever for the industry, with a total production volume of almost 802 million euros, although exports this year were already 0.3% lower than last year. The restructuring of the automotive industry, which led to a reduction in orders and increased competition from Asia, caused great difficulties and the following years went downhill. Interrupted in 2022, the year that ended with production and export growth of 1.5% to 605.2 and 505.3 million euros respectively. “2023 will bring growth, but still very weak and far from 2018 levels,” acknowledges the associative leader.
Portugal today occupies the top 3 in the sector, together with Germany and Italy, the eighth largest producer in the world. Germany (21%), Spain (16%), France (13%), USA (6%), Czech Republic (6%) and Poland (4%) are the main destinations for national exports.
This is an industry mainly made up of small and medium-sized enterprises, but with a great weight of small units, and which lives in a world of giants: upstream are suppliers, namely steel, a sector “with enormous power”, and downstream are the customers , the automotive industry’s first-tier suppliers. Growing up is vital. “We have a very polarized business fabric, we need to stay at the forefront of technology and find solutions for productivity gains and scaling to compete in the international market. Because the market is emerging, but with much lower price references than we are used to European Manufacturers have realized that dependence on the Chinese market is dangerous and want to focus a significant part of their purchases on production on the community market, but at Asian-level prices,” regrets Nuno Silva.
Mergers and acquisitions are welcome and while there have been some, they are not enough. It would be ideal for the association if companies find collaborative platforms. “There are already some examples of companies coming together to negotiate raw materials and find ways to optimize technology and knowledge. It would be very interesting if there were also platforms for understanding at a commercial level, but I have seen many doubts that this will be achieved in Portugal”, defends.
The decapitalization of companies is another major challenge, as after three years of difficulties they have “insufficient working capital to grow”, a situation exacerbated by “the imposition of payment terms that are difficult to bear”. The solution, Cefamol argues, should be to expand the companies’ activities from upstream to downstream.
“We are too specialized in the specific molding process. We have to work upstream in product development, participate in parts design with customers, and we have to work downstream in plastic parts production. It is a path that needs to be done, and it is already being done by large groups, or we will always be in a subcontracting situation. But again, the issue of scale is decisive,” defends Nuno Silva.
In terms of company capitalization, Cefamol “cooperates with Banco de Fomento in that the existing active lines within the sector can be used with adapted criteria”. It is also working to educate companies “so they understand the new business models and ways of working”, as well as trying to create “cooperation forums” in the industry.
In terms of business sector diversification, Nuno Silva admits that the industry intends to reduce its dependence on the auto industry, but recalls that it will always be a relative decline, of four or five percentage points, no more. “There is no other industry with the product turnover that exists in the automotive industry. A mold made for furniture or medical devices lasts seven or eight years, the automotive industry works two or three because right after that comes a restyling of the model that generates the need for new molds,” he explains.
The revolution in mobility and the commitment to different types of motorization is good news for the mold industry. “The more models the better, more molds are needed,” he defends.
These and other challenges in the sector will be discussed at the sector conference, scheduled for 17 and 18 March. “Shaping (in) a changing world” is the theme chosen this year at a meeting taking place for the first time in Oliveira de Azeméis. More than 300 participants are expected.
Source: DN
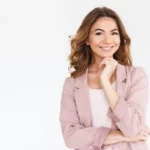