What is your vision of CSR issues?
Sustainable development ((Sustainable development | Toyota Material Handling (toyota-forklifts.fr)) is a central axis of the strategy of the Toyota Material Handling Europe group. For ten years, our parent company has set ambitious goals for all countries and encourages us to lead the industry transition, which is why the group has joined the United Nations “Getting to Zero” campaign, through which the company commits to setting science-based emissions reduction targets , throughout its value chain, to limit global warming to 1.5°C above pre-industrial levels Halve its greenhouse gas emissions by 2030 and achieve net zero emissions by 2050. This It is our strategic vision.
At the operational level, we work hand in hand with EcoVadis, which measures the effectiveness of our actions. The organization gave us the highest score, Platinum, for the second consecutive year. So we’re heading in the right direction…
What are your CSR actions?
We have established 3 priority topics:
– first and foremost, the health and safety of our employees. In this area, we comply with the ISO 45001 standard (Occupational Health and Safety Management). We have developed safety quarter hours to make our employees aware of health, safety and environmental issues each month and are dedicating 7,500 hours of safety training for our technicians this year (FY23) and 19,000 hours in total for all employees . Every year we organize a week dedicated to quality of life at work for all employees and managers.
– second axis of our strategy: minimize our impact on the environment. We take into account the environmental impact of our trucks at all stages of their life cycle: their development, their production, their use (our R&D&I focuses its efforts on minimizing the energy consumption of our trucks), and finally their elimination. We innovatively manage vehicles at the end of their useful life, ensuring that almost all their materials are reduced, reused, recycled and recovered. We recycle 90% of our waste. On the other hand, we audit each of our reconditioning agencies so that they adopt, as far as possible, the best Lean management practices and thus reduce waste as much as possible. Their energy consumption is also audited and minimized as much as possible. In addition, for 4 years, our car fleet has been made up of 100% hybrid vehicles. Finally, we are in the deployment phase of 3,000 m² of solar panels on the site of our headquarters located in Bussy-Saint-Georges (Seine-et-Marne). Our goal is zero emissions by 2050.
-last axis: the optimization of our internal processes. In particular, we have made good decisions in terms of after-sales service. Specifically, there is never more than 25 km of distance on average between the customer and the technician. This allows us to limit the carbon footprint of this activity. Along the same lines, we take care to put 95% of the trucks back into service in the first intervention, which avoids round trips.
Has your business model changed?
In the past, we sold cars. Now we sell solutions.
Previously based on the sale of new equipment, our model is in the process of evolving towards rental. Nearly 60% of the trucks we offer our clients are for rent, of variable duration and more or less flexible.
Most of the cars that return to us after being rented benefit from a second life, thanks to reconditioning. We have become experts in Certified Pre-Owned (Used Forklifts | Toyota Material Handling (toyota-forklifts.fr)) and put refurbished equipment back on the market with original and guaranteed spare parts.
We are also positioned in autonomous cars (Automatic Forklifts | Autopilot | Toyota Material Handling (toyota-forklifts.fr)), a market that is opening up. Thus, we increase the number of pallets handled for our customers.
Therefore, we are committed to meeting the productivity requirements of our customers, which requires a change of model, more focused on renting the right equipment at the right time and developing new services.
The digital revolution is taking the industry into the 4.0 era. What about your forklifts? They are connected?
Our shopping carts have been connected as standard since 2018, with our I_Site solution. This makes it possible to track all your data, accessible from a smartphone: the identity of the operator that used a truck, the hours of use, the level of charge of the battery, if it has suffered shocks, etc. Preventive maintenance is also possible: the data is retrieved centrally and the after-sales service will contact the customer to warn him that the truck needs to be repaired before it breaks down. This optimizes the management of the machine pool and is done in full compliance with the GDPR.
This content was produced with SCRIBEO. The BFMBUSINESS editorial team was not involved in the production of this content.
Source: BFM TV
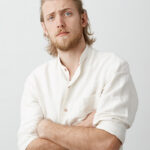