What is the mission of your company?
Our company was first called Hirex Engineering when it was founded in 1993. We then became part of Alter Technology Group, which had three other entities, including two in Spain and one in Scotland. The company was acquired in 2011 by the German certifying group Tüv Nord. We kept the Hirex Engineering name until 2020, then we became Alter Technology France.
Technical profiles (engineers or technicians) represent approximately 75% of our workforce. The rest is dedicated to our support groups. Alter Technology France realizes additional tests aimed at different equipment manufacturers, providers of electronic solutions based on semiconductor components. We test electronic components in so-called “hardened” environments, in extreme temperatures from -165°C to +310°Cradiation, humidity, saline or vacuum environment, vibration, shock and acceleration or any combination of the above conditions.
These tests are performed within the framework of a certain mission profile and for different applications. Of the total components tested, 58% are intended for the space sector, 25% for aeronautics, 10% for the automotive industry (electrification) and 7% for the industry or nuclear industry.
What are your tests doing? Can you give us examples?
In the domain of space, component qualification tests they are carried out in relation to particular missions: lifespan, altitude, even tilt. This last altitude criterion is also very important for aviation and automobile, in particular for radiation aspects. temperature tests They are necessary when the environment has extremely low or high temperatures. This is the case of an oil drilling, which is close to 230°C. Therefore, electronic components must be tested to ensure that they can withstand that heat.
How are its various tests carried out?
All our tests are carried out with specific equipment. we tried also wafer chips (very thin plate of semiconductor material of different diameters) finished components only, encapsulated in a plastic or hermetic case. Our site also has three laboratories:
- The Component Technology Analysis Laboratory (LAT). In case of failure in the tests, we perform a failure analysis. We also look at the construction of the component, to see if it can (or cannot) be used in a hardened environment. Finally, the LAT allows us to reverse engineer: we study the component to determine its inner workings and therefore understand if the technology can be used for hardened environments;
- The component testing laboratory and reliability testing of these components (LTE). These are electrical tests, whether the product is analog, digital, passive, discrete, power, and in particular so-called high-separation power components such as GaN (gallium nitride) and SiC (silicon carbide). We also test wafer chips there and perform reliability tests. This laboratory also allows us to carry out Mechanical vibration, acceleration and shock tests.. They are useful for ensuring, for example, that an electronic component is well-suited to a mission on an Ariane-type rocket. Finally, we can carry out environmental tests (thermal cycle, thermal shock, humidity, etc.);
- The Radiation Lab (Single Event Effects, SEE). He directs the radiation tests. In the first place, it involves simulations to visualize what the radiation dose that the component will receive in a given environment will be. We check beforehand if it will be able (or not) to resist it. This problem affects space and aviation as much as it does on earth. It is about the electronics present in vehicles. Therefore, we monitor radiation that directly impacts electronic components. Then tests are done depending on the environment using heavy ion accelerator for space, and protons and neutrons for aeronautics. On the automotive side, it should be noted that a new demand is appearing, since a terrestrial neutron can disturb the operation of a car. Hence the interest of these tests, knowing that automotive suppliers and car manufacturers qualify cars up to 4,000 m altitude.
How do you respond to the shortage of electronic components?
we do falsified trials. Given the lack of components, the broker (the intermediary between the seller and the buyer) has become a second source of supply. Today, large entities use it to ensure their production despite everything, even if it means add additional tests to verify batch origin and reliability.
All our tools (technological analysis of components, electrical test, reliability test) determine whether the batch received can be (or not) used by our customers. We are attentive to the chip and its serial number, as well as its assembly and encapsulation.
What do you think are the biggest challenges ahead of you?
The biggest problem ahead is integration of electronic components. New technologies integrate more and more functions on the same chip or on the same silicon-type substrate or other printed circuit-type materials. However, it will soon be necessary to find the corresponding team to test these new types of integration. Generally, there are two types of semiconductor integration:
- system-on-chip (SOC): at the chip level, with adapted technology and functions integrated into the chip;
- system in package (SIP): with several chips mounted on the same substrate, then encapsulated in a classic plastic box or also called a Chiplet.
Given the evolution of the sector, we will find a mix of various technologies at the level of a system in package. The integration will then be vertical 2.5D and 3D, always with more functions. It will be difficult to test this new type of product. This complexity can drive up the prices of test equipment.
Speed is another difficulty.. Everything is speeding up. We are already seeing this with components of autonomous vehicles, which operate at 77 Gigahertz, and satellites with KA and KU bands for telecommunications. In addition, the components of satellites are becoming more and more complex. More and more data transmitted to Earth. We need to quickly adapt and provide testing solutions that are effective enough to monitor these industries. Finally, the mix between photonics (the light) and radio frequency (radio frequency) represents another integration difficulty to successfully transfer information, both for testing and assembly.
To conclude, what is your vision of the semiconductor market?
It’s time to regain European sovereignty in semiconductors. Governments believe that we are capable of producing 5 or even 7 nanometers (a product found in our phones). However, to reduce the cost of semiconductors, you first need volume. I’m not sure there is a European market for these sizes. In my opinion, we first have to have all other technologies (14, 16, 22, 28 nanometers, etc.), most used in Europe as far as digital components are concerned, but we also need other technologies for power, such as GaN and SiC, as well as technologies for RF.
We also need experience to compete directly with the Asian market. That is why it is important to train the new generations of engineers in these issues, from school.
This content was produced with SCRIBEO. The BFMBUSINESS editorial team was not involved in the production of this content.
Source: BFM TV
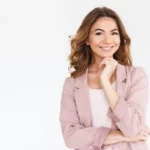