About half of companies in the textile sector are experiencing sales declines compared to the same period last year and 80% have cut profit margins to offset the rise in inflation and production costs, namely energy. More: Nearly two-thirds of companies have reduced order books in this last quarter of the year. The data, which are still preliminary, come from the most recent survey of the activity of the Association of Textiles and Clothing of Portugal (ATP), whose president speaks of a “very difficult” situation that will affect the survival of many companies could endanger.
“If the war continues and gas prices remain high, companies that use gas intensively will not stand a chance if they are not helped,” admits Mário Jorge Machado, who prefers not to explore this reality much, stressing that “it is a scenario that not even worth talking about, it would be catastrophic for the country and for the industry”. At the opening of the recent European industry convention, the ATP chairman warned of the risk of a “massive purge in business, where only the fittest can survive”, stressing that “any bankruptcy is a victory for Putin, who uses gas as a economic weapon”.
The businessman is now a bit more enthusiastic, as gas prices have started to fall, from 100 to 40 euros per megawatt hour (MWh). “There are already positive signs here that the great fear of gas shortage is starting to subside and that’s very good because it gives confidence again,” he says. But he acknowledges that we live in times of “extreme volatility” and that the situation could change at any time.
As for the research data, which shows that 29% of companies have reduced their margins by 10 to 30% and more than in the case of 12% of respondents, Mário Jorge Machado assures that this is no surprise. “Brands are buying less and that was noticed from July onward by the combined effect of inflation on rising prices and fears of the recession coming up,” he says.
The truth is that the situation does not affect everyone in the same way and there are 33% of respondents who register an increase in sales in the last quarter compared to the same period in 2021. Most with a growth of up to 10%, but there are also 2% of companies with a turnover increase of more than 30%.
Mid-range brands will suffer the most, ATP admits. The luxury market is on the rise and there is a great desire to exchange factories in Asia for Europe.
“Fortunately, there are market segments that are doing better, namely everything that has to do with luxury. On the other hand, home textiles are more affected than the rest of the sector,” he explains. The fact that they were among the most purchased items by the Portuguese during the pandemic, and because they are durable goods, helps to understand this less positive achievement.
Because there is no information on who buys the least, ATP admits it will be companies that operate in the mid-market. “Luxury is usually less affected by these situations and these companies want to move more of their productions from Asia to Europe and have no problem paying European prices. We have been approached by many European luxury brands in this regard.”, guarantees the association leader. Mid-sized brands “also want to produce in Europe, but have more trouble finding producers within their price range,” he emphasizes.
It is this increased demand, also for reasons of sustainability, that gives confidence in the future. “The situation is subjunctive, but structurally the sector has not had such a positive horizon since the 1990s as it has been this decade with the reindustrialization of Europe and the growing demand for sustainability and the circularity of products, areas in which the textile sector has invested heavily and that will yield even better results if the digital passport is mandatory,” he says.
This document, which according to Mário Jorge Machado will take two to three years to be implemented by the EU, will contain information on the environmental sustainability of products, so that consumers can make informed choices. “It will be a real revolution,” he promises.
But first you have to survive the energy crisis. Survey data shows that electricity costs have increased for 93% of businesses in the past three months, with a third of them increasing by more than 50% and a further third increasing between 30 and 50%. The reality is different with natural gas, as only 33% of companies use this energy source. Of this universe, the largest share, 14%, registered a price increase between 100 and 250%, 5% saw the bill rise to 500% and another 5% above that.
“It is the finishing companies that have this impact, but if they close, the whole chain will be at risk. Machado, who estimates that there are about 100 finishing units in Portugal that will provide employment for about 10,000 people, but that the 130,000 workers in the textile and clothing sector, underlines that aid to companies is still not enough, despite the increase to 40% in the eligible costs and the increase in the aid limit from EUR 400,000 to EUR 500,000.
“If the war ended, 40% would arrive, because even with losses, companies would consume them in the following years. To keep the war and the high gas prices, we have always said support would be in the order of 70% and that limit should be two million per company,” ATP defends. The investigated possibility that negative EBITDA, caused by the increase in energy costs to five million euros, could be covered “is a perfectly logical measure”.
Ilídia Pinto is a journalist for Dinheiro Vivo
Source: DN
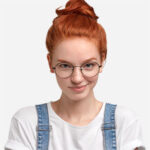